Defects and elimination of clip feeder
2020-06-23(1955)Views
As a high-precision feeder specially adapted to the use of high-speed punch presses, the clip feeder will inevitably have defects due to improper operation, incorrect debugging, machine wear and other factors in the practice process.
Defects 1. The data of the clip feeder is not sent out or sometimes is too short. There are five reasons for the occurrence:
1. When debugging the clip feeder, the material thickness is not adjusted correctly (too thin) or the clamping force is not good.
Handling method: According to the debugging method on the manual of the clip feeder, adjust the plate thickness of the clip feeder from scratch (disassemble the plate thickness adjustment bolt, and then rotate the scale ring according to the thickness of the data to align and score). Pay special attention to the need to adjust the material thickness from scratch when changing the thickness of the data, so as to ensure the proper clamping force.
2. The clip feeder cannot loosen the clip, and the data is squeezed between the two clips.
Handling method: adjust the plate thickness from scratch.
3. The material itself has twists and waves and rough edges.
Handling method: replace the normative data.
4. The feeder has been used for a long time, and the wear of the components causes the clamping amount of the feed clamp to be ineffective.
Contact the after-sales personnel for repairs.
5. The feeder has been used for a long time, and the wear of the components causes the loosening of the stopper clip.
Contact the after-sales personnel for repairs.
Defect Two. The material of the clip feeder is not loosened or retracted. There are two reasons:
1. The relaxation time setting is incorrect.
Handling method: Adjust the relaxation time from the beginning of the clip feeder according to the debugging method on the manual of the clip feeder.
2. Present changes when using it at the time of relaxation.
Handling method: Recognize the loosening of the tightening bolts from the beginning.
Defect Three. The feeding distance of the clip feeder is long and short. There are six reasons for the occurrence:
1. The feeding time is incorrect
Handling method: schedule the timing belt and adjust the feeding time of the feeder.
2. The feeding cam or bearing in the feeder is worn.
Handling method: adjust the cam orientation from scratch or send for repair.
3. The guide pins or punches in the mold are too long to make the feeding time lack of 180 degrees.
Handling method: Shorten the guide pin or punch.
4. In-mold punch or shaped parts
Handling method: replace the high-stroke punch.
5. The clip feeder has a partial loosening of the rod seat
Handling method: re-tighten the fixed nut of the rod base.
6. The gear box gear is worn or the drive spindle is loose
Handling method: adjust the handling or return to the factory for protection or update.
Defects 4. The feed distance varies when the clip feeder is linked, and there are three causes:
1. The transmission gear of the clip feeder is worn or the transmission spindle is loose
Handling method: adjust the handling or return to the factory for protection or update.
2. The feeder has been used for a long time, and the wear of the components causes the clamping amount of the feed clamp to be ineffective.
Contact the after-sales personnel for repairs.
3. Loose belt
Handling method: adjust the belt tightness from the beginning.
Defects 5. The data of the clip feeder is twisted between the feeder and the mold. There are two reasons for the occurrence:
1. No bridge guide material pressing equipment.
When thinning the data, the distance between the feeding plate of the clip feeder and the lower template is necessary to make the material guide and press equipment, so that the data is not tortuous as a guideline.
2. The height difference of the feed line is too large
Adjust the feeding height of the feeder and the height of the mold data line.
Defects 6. The data is skewed between the feeder and the mold. There are three causes:
1. The mold data line and feeder are out of position.
Handling method: start the mold from the head.
2. The material itself has twists and waves, rough edges, etc.
Handling method: replace the normative data.
3. The material clamp is not flat and the feeding is skewed
Handling method: study material clip or send for repair.
Recommended News
-
Defects and elimination of clip feeder
As a high-precision feeder specially adapted to the use of h...
-
The difference between pneumatic relaxation and mechanical relaxation of servo feeder
The biggest difference between the mechanical NC feeder and ...
-
Long Harmony Automation Equipment: What is the reason why the feeder is popular
The three-in-one feeder is divided into three types: standar...
-
Long Harmony Automation: Advantages of various feeders
Air feeder: The air feeder is the earliest feeding equipment...
Contact Us
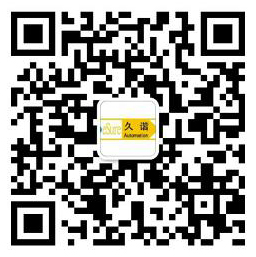
Service Hotline+86 13580817073
—— WeChat communication